Analysis and selection of SMT mounter
1、 Preface
Automatic component placement machines play a very important role in the assembly of circuit boards. However, when purchasing such equipment, the assembly industry does not have sufficient knowledge on how to select a suitable and fully functional machine. In this article, we will discuss the functions of the component placement machine one by one. After having this knowledge, it will be easy to select the appropriate component placement machine.
2、 Critical differences
In the face of the constant demand for portability of electronic products, the assembly industry hopes to meet this requirement by reducing the size of components and increasing the assembly density of circuit boards. In recent years, with the gradual adoption of cladding technology, the goal of module miniaturization seems to have been solved, but there are still some difficulties to be further confirmed. For example, although the pins used in the assembly of cladding are low temperature eutectic tin balls, which are similar to the traditional surface adhesion technology, it is not so that the module placement machine can easily be applied to the cladding technology, There is still a gap between the technology of the component placement machine used in the traditional assembly and the use of the cladding. The main difference is whether it can still provide the same assembly alignment quality as in the past when using the components with smaller spacing (less than 0.012?) and smaller end. The component placement machine must have a more accurate vision and alignment system to meet the needs of the cladding technology.
In addition, the common cladding spacing is 0.004?, The diameter of tin ball is less than 0.002?, Because before the reflow process, the components are temporarily attached to the circuit board with flux (FLUX). If the current components are of small spacing, the relative amount of flux will also be less than that of other components with large spacing. If the flux is not perfect when it is wet, or cannot provide enough adhesion to fix the original on the welding pad, the welding quality will be poor. The problems mentioned above point out that the problems faced by the module placement machine when it is applied to the cladding technology are quite complex.
Generally speaking, one part can be applied at a distance of 0.004? The speed of the component is about 8 sec/part, and the whole dynamic process includes the absorption component. The price of the mobile and visual system alignment function is about $400000 to $500000. The difference lies in the requirements of the selected equipment. Although such equipment can meet the current requirements, will it still be applicable in the future? This depends on continuous observation of the development of future component forms.
3、 Resolution and accuracy of module player
Obviously, resolution and accuracy are very important parameters for the application of the component placement machine in fine-pitch parts. Generally speaking, accuracy is a function of the precision resolution of the vision system and the stability of the device in the X -, Y -, and Z – directions. In short, during the component placement action, the placement suction head moves to the set position in the 3-D direction, The system must be able to “see” and confirm whether the position of the components to be placed is correct.
The resolution of all tested component placers must be 0.00004? To 0.00008? Within this range, and the accuracy is about 0.0004? To 0.002? This result shows that the smaller the data is, the better the use of small spacing. Other parameters (such as the accuracy of the assembly nozzle at full speed and the standard of the alignment error between the solder pad and the solder ball) will affect the level of the equipment. In this view, the distance between components that the current high-speed machine can load is 0.0034? To 0.012?, We can deduce the minimum allowable component spacing during assembly by the following formula: accuracy * (100/percentage of alignment error between solder pad and solder ball) * 2=applicable spacing ex: 0.001* 100/25*2=0.008?
From the above example, the accuracy is 0.001? With 25% alignment error, the module placement machine is suitable for use at a spacing of 0.008? If the error tolerance adopted by the supplier is 33%, the component spacing used by the above machine is 0.006? Yes.
4、 Accuracy and verification of component placement machine
The accuracy and continuity of the module placement machine can be verified by the chrome on glass method. The method is to make a line on the glass sheet by soldering, and then place the glass sheet in the module placement machine. Use the substrate and the basic point of the module placement position to guide the machine alignment. After the entire assembly process is completed, through the inspection of the optical microscope and the measurement of the cursor ruler, for multiple positions, Then judge its accuracy by moving at full speed.
The inspection method of chrome on glass is an artificial process. However, it is still a quite effective verification method on the issue of whether the machine has a certain degree of accuracy. It is very important that when the machine is just started, the action potential of this manual alignment accuracy confirmation must be quite accurate, so as not to affect the accuracy of the subsequent operation. However, not all such devices will perform similar actions at the beginning, and not every device is attached with a glass plate with a soldering scale to help correct the accuracy.
In addition, the thermal stability of the module placer will also affect its accuracy. For this reason, Jabil’s crystal clad module placer uses granite abutment and ceramic support beam to reduce such impact. In this case, if the equipment is brave enough to deal with the spacing of 0.004? It is very important whether the components can be self-thermal corrected. Although some manufacturers emphasize that their equipment does not need such correction, the importance of thermal correction is also emphasized from time to time in the relevant plays.
5、 Placement rate
Generally speaking, the speed of placement does not include the steps of circuit board transportation and visual alignment, so the speed announced by various manufacturers is quite fast, but if the above two actions are included in the calculation, the speed will decrease rapidly. For example, if these two items are not included, the general rate is about 2000 pph, but if these two items are added, the rate will drop sharply to 800 pph.
Looking around, the current assembly placement machine takes about 2.5 to 8 seconds to perform the extraction of components, soldering flux, visual alignment, and placement of parts. If the relevant processes such as soldering flux, solder paste, or conductive adhesive can be separated to make it not operate in the assembly placement machine, the placement time can be effectively shortened. In addition, the same effect can be achieved if the moving distance of the suction nozzle can be shortened.
6、 Conveying
Generally, when the circuit board moves at a high speed in the component placement machine, the components are adhered to by adhesive flux as much as possible. If the movement, start or stop of the circuit board is too large, it is likely to cause component displacement and confusion. Therefore, the conveying system must have individual speed control units in three different areas during the transportation of the circuit board.
In the first area, the system must transport the circuit board to the predetermined position at high speed as possible (in this part of the components, the solder paste is usually used to provide sufficient viscosity to cope with high-speed movement). This area is mainly to transfer the flip chip onto the circuit board.
The second area (usually called the assembly area) will move at a slower speed because the flip chip has completed the assembly in this stage.
The third area (usually referred to as the detachment area) is to send the circuit board out of the component placer. Flux plays a very important role in this area. Increasing the amount of flux will provide greater adhesion of flip chip, which can transport the circuit board at a higher speed. This can also improve the production capacity, but it will also face some problems, that is, if it is not combined with the cleaning system, the residual flux will cause poor flip chip welding.
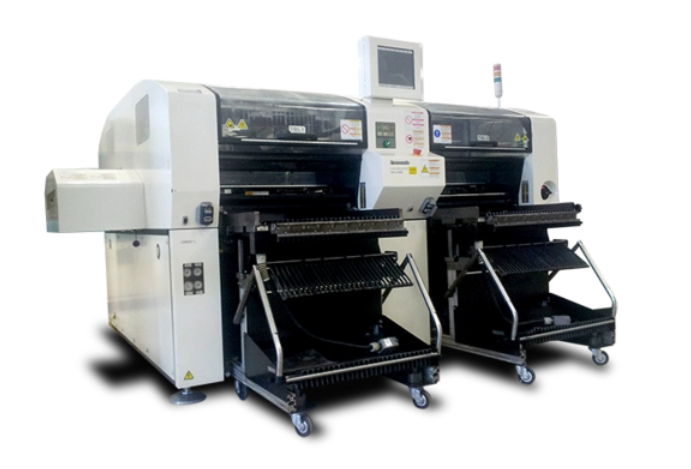